Kistler Group Product
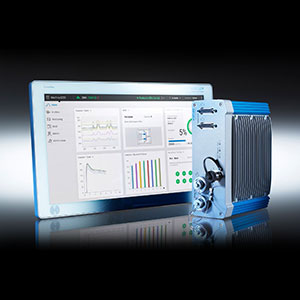
Kistler systems: the ideal basis for enhanced transparency in networked injection molding production
Benefits of Kistler systems:
- Zero-defect production
- Quality costs are cut
- Optimal process efficiency
- Process reliability is enhanced
- Cycle times are optimized
- Staff costs are reduced
- Plant efficiency is increased
- Rapid amortization (RoI)
- Industry 4.0
- Networking
- Data management and optimization
The Industry 4.0 vision has already emerged as a distinct reality in the injection molding sector. The new approach to production focuses on consistent digitization – leading to enhanced product quality and increased cost-efficiency. Injection molders equipped with Kistler systems for process monitoring and control are ideally placed to meet the requirements for digital networking. Information networking and data management are gaining importance as we advance towards Industry 4.0.
Quality requirements for injection molding are constantly increasing, so permanent control of the entire production chain is essential. Kistler presents ComoNeo and ComoDataCenter: two system components that offer the best possible basis for achieving this goal – and they are perfectly suited to novices as well as experienced users.
The new features integrated into ComoNeo have been specifically developed to meet the requirements that are arising as this happens. First and foremost among these new features is the ComoNeoRECOVER Restart Assistant now integrated into ComoNeo, which allows efficient reproduction of established processes when changing machines. But there are many other innovations as well: for example, the system now supports the standard for injection molding production. Integration of OPC-UA in ComoNeo also makes it possible to implement hot runner control as an entirely standalone solution, without an additional PC. The benefit: significantly less effort is required because the entire setup process is simplified.
Another new feature for ComoNeo: an integrated feature that allows reliable advance predictions about every part to be produced, so the full bandwidth of cavity pressure monitoring methods is available – from monitoring of process fluctuations and manual or automated EO monitoring (with ComoNeoGUARD) through to online quality prediction (with ComoNeoPREDICT). This is a high-end solution for direct calculation and evaluation of part characteristics.
In a nutshell: by adding these new features to ComoNeo and ComoDataCenter, Kistler is paving the way for yet more future improvements to product quality and cost-efficiency in injection molding production.
Click herefor more information on Process Monitoring and Controls by Kistler.