新闻
让事情变得更好。
发表于03/08/2021.
为什么,怎么做,你应该做什么来把ML从一个流行词变成你生产线上的现实
多年来,我的工作与现在的情况大不相同。这并不奇怪,考虑到我从设计和制造半导体和光电子产品转到运营SW初创公司。实际上,我在那些年里遇到的很多挑战都与创建一家名为Vanti Analytics的初创公司有关。
那么,当我负责交付一个复杂的系统、增加产量并坚持严格的质量要求时,我的日子是怎样的呢?通常情况下,我们是在调查一种现象或试图找到失败的根本原因。老实说,我一直觉得我们做得不够好。更具体地说,我认为我们花了太多的时间和资源来得到我们需要的答案。无论是用于实验的实际材料,还是一个专门的工作小组,在实验室里花很多时间的专业人员。回顾过去,我们在快速高效地解决问题方面最成功的例子是,我们设法利用制造业务产生的数据产生的可操作的见解。
我有一个难忘的例子,我们的一个光电元件经常发生短路问题。它是偶尔出现的,似乎没有任何可解释的原因或模式。我们无法预测它何时会发生以及如何预防它。调查持续了好几天,其间我们每天进行多次头脑风暴,进行各种各样的测试——电气、环境、视觉检查等等。最终,我们发现测试设备为组件供电的一种方案极有可能导致过热并最终导致设备故障。一旦确定,解决方案就会相对迅速和直接;电源信号的重新配置立刻解决了这个问题。
但这只是现代制造业环境中每天都发生的众多问题之一。主要原因是产品越来越复杂,制造它们的技术也越来越复杂。制造过程中使用的装配和测试程序与最终产品的质量和功能紧密结合。对于跨越通信、汽车和消费行业的高端电子产品尤其如此。
为确保最高质量的最高生产力,生产团队不断工作,以更好地控制流程。目标总是能够在过程中尽早预测和防止故障。测试方案和控制限制由质量和工艺专家确定。
然而,即使在性能最好的制造环境中,仍然有隐藏的价值需要挖掘。例如,它可能是一个系统性的失效机制:“当放置位置是X,测试#4,#8比平均水平低10%时,失效概率会高30%”。这是一个简单的控制窗口/规则无法检测到的洞察力。另一个例子可能是实时检测异常组件,需要一组不同的工艺参数(例如,焊接温度)才能正常工作。
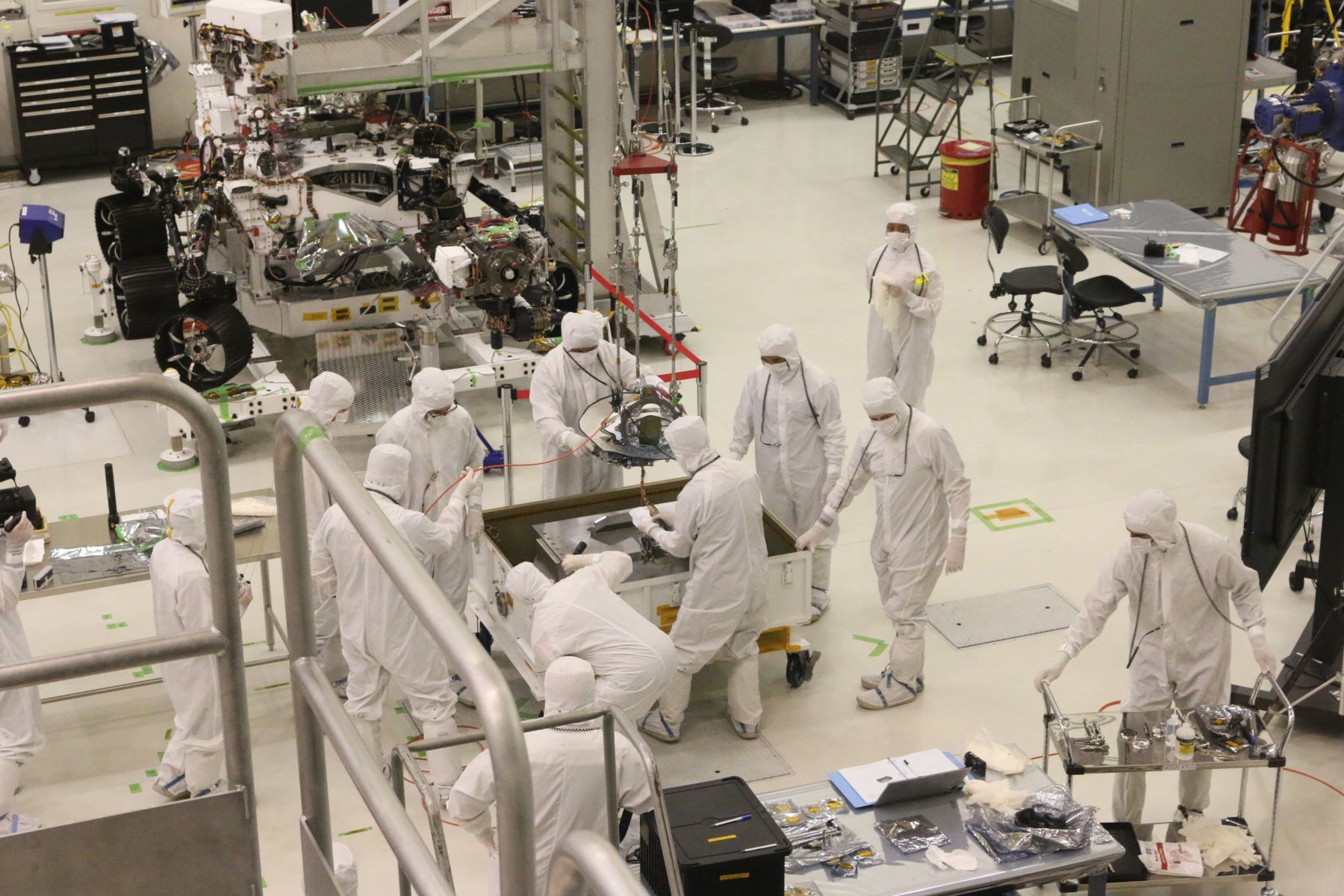
那么,我们如何确保以可扩展的方式保持优化的生产环境呢?增加更多的资源(设备和/或人员)是昂贵的,在许多情况下,甚至是不可能的,因为制造专家很难找到。
这些方案为ML和AI技术提供了完美的合适。通过将高级学习算法与在每一步的生产操作产生的数据结合,我们可以学习产品的系谱,因为它们与其制造过程相关联。
有了对产品行为的如此深入的了解,我们现在可以检测到这些异常,甚至在它们发生在生产线内,甚至更糟,在发货给最终客户之后。
虽然检测异常对制造商来说意义重大,但真正重要的承诺是知道“为什么”和“是什么”——是什么造成了异常,需要做什么来纠正它,并防止它在未来发生。要做到这一点,需要结合领域知识和构建ML模型的可解释方法,但这是我们下一个讨论的主题(请继续关注!)
这种能力只是从制造领域的数据中释放巨大价值的第一步。接下来的步骤将使这些知识能够实时指导机器,执行自动RCA(根本原因分析),预测和优化多线路变化或现场服务,等等。
如何在实践中开始使用AI / ML技术效益?虽然它可能听起来非常令人恐惧,但它可能很简单。
让我们从最明显的开始;毫升需要数据。但这到底意味着什么呢?
在Vanti,我们定义了一个相当简单的框架和先决条件,让数据集通过与许多客户合作来看到ML的价值。
数据要求分为(如何不)三部分:
- 数据类型,我们说的是两种数据。产品和过程相关。与产品相关的数据包括生产过程中每一个步骤的所有测试和检验结果,记录为每一个单元或批次。它通常是表格数据,其中可能包括文本和数值,连续或离散。与工艺相关的数据包括由嵌入其中的机器或传感器配置和控制的工艺参数/配方。在这里,我们通常会看到时间序列数据,现代制造设备的标准输出。
- 可追溯性 - 这可能是难题的重要组成部分。我们应该确定为每个单位/批次/模块/等获得的相关数据点。学习产品的行为如果我们无法将参数与结果相关联。这同样适用于与进程相关的数据。时间戳应在不同的电台与生产流程之间可靠且一致。好消息是可通过S / N(批号)或其他标识符提供可追溯性。在某些情况下,需要产品树来识别每个数据点的源,但定义这些关系是在船上过程中的一次性精力。
- 数据量——这是一个经常出现的问题,有几个方面对答案有影响:数据集中通过/不通过单元的比率,数据集的“丰富度”——意思是,关键贡献者在数据中是否足够好地表示,标签的可用性(它是否包含已知失败的可靠指示)等等。也就是说,创建一个好的模型所需的示例的一个良好起点是每个参数(行~= 10 x列)有10个示例。与传统的ML技术相比,这是一个相当低的数字,但是使用我们专有的模型构建体系结构,我们已经多次看到这种工作。
一旦识别和提取了数据,构建模型的艺术就开始了。如上所述,学习产品和过程谱系以检测异常是大多数制造用例的核心。关于我们在Vanti解决这个问题的方法的更深入的回顾,请参阅我们最近的博客文章:如何检测生产中的未知异常。
好的,我们建造了一个模特,现在是什么?要在生产线中使用此模型,这意味着在实时地对潜在故障的单位或流程进行预测,我们需要一种方法来将收集的数据发送到模型,并将结果送回行。
一个简单的、经过验证的方法就是通过API与车间的数据库建立双向通信。通过一个标准协议,结果被发送到模型。然后将预测推送到客户选择的任何应用程序(直接推送到测试设备、运营商的手机,或者简单地通过电子邮件通知)。预测可以是“通过”/“失败”/“可疑”,在这个或任何其他格式的每一个单个生产单元。
但如前所述,这只是图片的一半。除了预测外,操作团队还需要接收可操作的信息。可能的洞察力是:“放置过程需要更严格的新批量限制。”洞察力也通过同一界面进行快速交付,并通过生产团队解决。
如果之前没有这样做,它可能听起来很复杂,但我们发现这个过程可以在几个小时内完成。在vanti,我们习惯于支持客户并与他们合作,建立第一个模型,并在几天内展示价值。
把我们放在一边info@vanti-analytics.com请求完整的指南(带有实际的数据样本和接口文档),或安排与我们的专家进行15分钟的通话。