Editorials
4 Common Robot Programming Challenges
POSTED 12/07/2022
| By: N. Adams, Product Marketing
When manufacturers are looking at transitioning their manual, labor-intensive applications to automation, a common concern that comes up is how the robot will be programmed
There are a few programming methods available. Two of the most common methods are teach pendant programming and offline programming software.
With the teach pendant method, an electronic control box is used to program the motions of the robot. The robot is moved into each desired position, and it is saved as a point in the program. The output is a program in the brand-specific programming language of the robot arm.
Alternatively, offline programming (OLP) software enables the user to program the robot on a computer, independently of the hardware, rather than taking the robot away from production. The user imports the CAD model of the part, uses the software to create path trajectories based on the part profiles, and can generate a program in a matter of minutes. OLP software also provides program optimization and validation through the virtual/simulation environment that matches the real-world robot cell to ensure the generated program is error- and collision-free.
The programming method can seriously impact the return on investment (ROI), so finding the optimal programming method for the application is critical for the customer to achieve optimal outcomes. Some common criteria when looking at the programming methods include:
Learning curve
If programming the robot is too difficult to learn, manufacturers are going to be reluctant to automate. The programming solution needs to be easy enough for current and future employees to grasp and understand.
Complex shapes
Complex part profiles can be hard to replicate. The programmer needs to have the confidence that they can reproduce the results consistently while maintaining accuracy.
High-mix, low-volume production runs
In high-mix, low-volume production runs, programming delays can have serious implications on delivery times and margins. If the production style is one that has a variety of parts in lower quantities, the programming method needs to be adaptable to rapidly change parts and cycle through different customer requests.
Accuracy and repeatability
Achieving consistent results can be critical to meeting customer expectations, especially in industries with very stringent requirements such as in aerospace. Repeatability can be an important factor to consider when selecting the programming method.
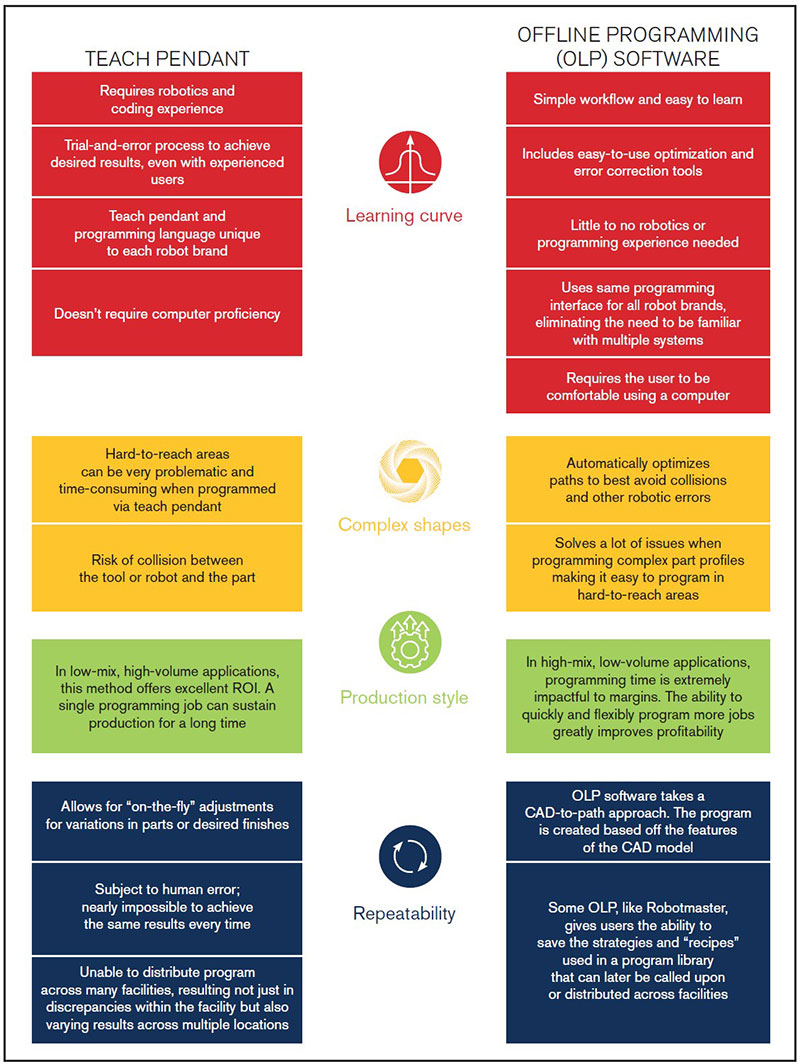
Teach Pendant vs Offline Programming (OLP) Software
Download/View PDF
Both programming methods have applications and circumstances for which they are better suited for.
In general, the easier it is to use the programming method, the faster it will be to program. Depending on part complexity, each programming method will take a different amount of time and pose different degrees of risk. Furthermore, the production style also affects how critical programming time is; the higher the mix and lower the volumes, the higher the benefits of programming using an OLP solution. Finally, if achieving repeatable results is essential to the business, a software programming solution may be the best method.
There are a lot of factors to consider when selecting the right programming method for your robot. OLP software is not the right solution for everyone but for many it is. We have a team of experts that would be happy to schedule a short discovery call to determine if OLP software is a good fit for your business.Chat with our experts.